La reedición de la norma internacional de productos para entubado continuo curado en obra, ISO 11296-4, supuso la introducción de una serie de modificaciones en el año 2018. Tras nuevos términos como grosor de pared de diseño y aglomerado se ocultan importantes adaptaciones necesarias para el sector, como se hizo evidente desde el principio. ¿Qué deben tener en cuenta planificadores, fabricantes, instituciones de ensayos y constructoras? A continuación publicamos un artículo especializado sobre cómo aplicar la teoría a la práctica que aporta transparencia.
Introducción
El entubado continuo curado en obra, una de las numerosas tecnologías para el saneamiento de tuberías, es el proceso de renovación más utilizado del mundo. ISO 11295 clasifica y describe, en general, las familias de técnicas.
ISO 11296-4, en combinación con ISO 11296-1, establece los requisitos y procesos de comprobación para el entubado continuo curado en obra (véase la Imagen 1). En la versión actual de la norma DIN EN ISO 11296-4 (2018-09) se han incluido cambios que aportan grandes ventajas en materia de precisión dimensional y homogeneidad de los indicadores mecánicos para todo el sector. En este sentido, es necesario explicar, desde un enfoque práctico, las definiciones relativas a los grosores de pared y el nuevo término «aglomerado».
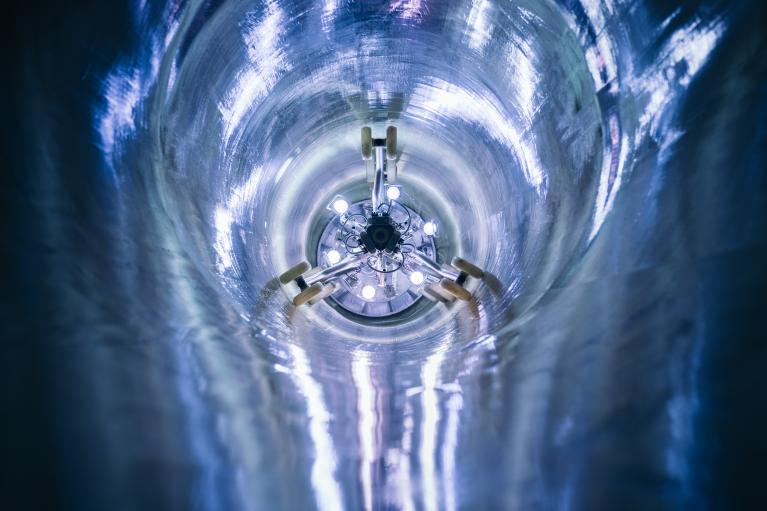
Imagen 1: Entubado continuo curado en obra
Planificación: Grosor de pared de diseño
Todo saneamiento de tuberías realizado con éxito comienza por la planificación por un/a ingeniero*/a o un/a asesor*/a certificado/a de saneamiento de canales. En un principio, es necesario efectuar, entre otras cosas, estrategias de saneamiento, planes de existencias, análisis y valoraciones del estado de las tuberías instaladas, cálculos de costes y beneficios, dimensionamientos hidráulicos, etc., cálculos estáticos teniendo en cuenta las cargas locales específicas (cargas de aguas subterráneas, tráfico y suelo, presión interior y sustentación) e indicadores específicos del material, para determinar el grosor de pared de diseño. En este sentido, se trabaja sobre la base del reglamento aplicable de la DWA para obtener el grosor de pared de diseño teórico y numérico necesario. Este es el grosor de pared mínimo que se debe aplicar y demostrar como estáticamente efectivo. El grosor de pared de diseño se determina sobre la base de las propiedades mecánicas, tales como el módulo E o la resistencia. Las capas de desgaste no deben formar parte del grosor de pared de diseño, es decir, se deben planificar adicionalmente.
A modo de ilustración, a continuación trabajaremos sobre el ejemplo de un grosor de pared de diseño de 3,8 mm calculado para un SAERTEX-LINER MULTI tipo S+. Este grosor de pared se deriva de los indicadores descritos en la homologación de DIBt. Dichos indicadores hacen referencia al grosor del compuesto (véase el punto siguiente).
Producción Grosor compuesto
Hasta ahora, todos los fabricantes debían demostrar el denominado grosor compuesto conforme a la norma DIN EN ISO 11296-4 (2011) y relacionar con dicho grosor los indicadores mecánicos. El grosor compuesto se suele denominar grosor de pared compuesto, según la nomenclatura de las homologaciones de DIBt, y hace referencia al laminado en sí (sistema de resina + fibra de vidrio), descontando las llamadas capas ricas en resina (véase la Imagen 2). Por razones de producción y diseño, el grosor compuesto suele ser diferente para cada fabricante de entubado continuo. Para los fabricantes de entubado continuo, no es económicamente concebible ofrecer todos los grosores deseados en intervalos de décimas de milímetros. Por tanto, los proveedores del mercado han definido intervalos de grosores de pared fijos, cuya producción resulta idónea para el fabricante en cuestión. SAERTEX multiCom, p. ej., se ha marcado para las aplicaciones de flujo por gravedad, independientemente del tipo de resina, grosores compuestos nominales con valores de milímetros enteros (3,0 / 4,0 / 5,0 hasta 15,0).
En nuestro ejemplo, el grosor compuesto nominal elegido sería de 4,0 mm.
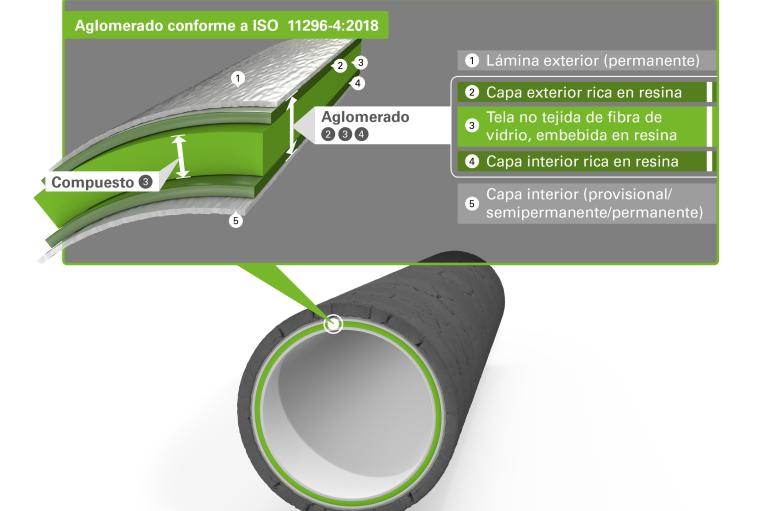
Imagen 2: aglomerado frente a compuesto
Indicadores mecánicos: grosor del aglomerado
Con arreglo a la norma DIN EN ISO 11296-4 (2018) actualmente vigente, los indicadores mecánicos de los revestimientos ya no hacen referencia al grosor compuesto, sino al grosor del aglomerado. El grosor del aglomerado se calcula muy fácilmente a partir del grosor total, restando de esta medida las láminas termoplásticas interiores o exteriores. En el futuro, los fabricantes indicarán el grosor de las láminas en las hojas de datos técnicos de los revestimientos. De este modo se elimina la medición de las capas ricas en resina, extremadamente inexacta y costosa. Al mismo tiempo, se incrementa la exactitud de los indicadores para el módulo E y la resistencia y se elimina la anterior posibilidad de un error de cálculo. El grosor de aglomerado es el grosor completo del laminado y, al contrario que el grosor compuesto, no solo incluye las capas con una proporción de fibra de vidrio en el núcleo, sino también toda la resina situada entre las láminas. Esto implica cambios considerables en el cálculo de los indicadores mecánicos en pruebas de flexión de tres puntos o en las pruebas de presión en el vértice. A partir de ahora, los revestimientos tienen otros indicadores para el módulo E y la resistencia. Pero, dado que también cambia el grosor nominal del revestimiento, la planificación de una aplicación determinada, al final, dará como resultado los mismos revestimientos con idénticas rigideces anuales que los cálculos realizados según la versión anterior de DIN EN 11296-4.
El grosor del aglomerado, compuesto por el laminado más la capa rica en resina, es, en principio, mayor que el grosor compuesto. Los indicadores mecánicos, tales como la resistencia a la tracción por flexión o el módulo E serán menores (véase también el informe del Dr. Ing. Ricky Selle y Dr. Ing. Nils Füchtjohann).
Terminología conforme a DIN EN ISO 11296-4 (2018-09)
Aglomerado: Combinación del sistema de resina curado (3.1.16), el material portante (3.1.2) y/o el refuerzo (3.1.15), excluyendo las láminas interiores o exteriores
Grosor de pared medio del aglomerado: como mínimo, el grosor de pared de diseño (más el grosor de la capa de desgaste correspondiente)
Mínimo grosor de pared de diseño del aglomerado: como mínimo, el 80 % del grosor de pared de diseño (más el grosor de la capa de desgaste correspondiente), o 3 mm, aplicándose el mayor valor
Grosor de pared de diseño: grosor de pared de diseño necesario del aglomerado (3.1.6), excluyendo la capa de desgaste (3.1.1), que se determina mediante cálculo estático
Grosor de pared nominal de CIPP: un valor derivado de una serie de grosores de pared diferentes de entubado continuo de revestimiento, que se calcula a partir de la suma de los grosores de las distintas capas de materiales en estado «M»
Grosor de pared total: Grosor de la manga curada una vez instalada en estado «I», compuesto por el aglomerado (3.1.6) y todas las láminas semipermanentes (3.1.17) y permanentes (3.1.13)
Producto CIPP, producto de manga curada una vez instalada: manga curada una vez instalada de una estructura determinada fabricada a partir de un revestimiento de determinados materiales, con una estructura de pared definida individualmente para cada combinación de diámetro y grosor de pared y que se impregna con un sistema de resinas especial (3.1.16) y se instala con un proceso determinado
Capa de desgaste: Capa interior del aglomerado con un grosor declarado, aplicada como capa de sacrificio para el desgaste previsible del producto de CIPP (3.1.3).
Manga: manguera flexible compuesta por material portante (3.1.2), sistema de resinas (3.1.16) y todas las láminas y/o refuerzos (3.1.15), en el estado en que se produce antes de su instalación en la tubería en renovación
Terminología conforme a DIN EN ISO 11296-1 (2018-09)
Estado «M»: Estado «de fabricación» (en inglés: as manufactured), es decir, antes de que se produzca el tratamiento de los componentes en la obra con el proceso de renovación correspondiente.
Estado «I»: Estado «de instalación» (en inglés: as installed), es decir, en un estado definitivo después del tratamiento de los componentes en la obra, como consecuencia del proceso de renovación correspondiente
Al mismo tiempo, aumenta también el grosor de pared en los cálculos, compensando totalmente este efecto.
Para las aplicaciones de flujo por gravedad, SAERTEX multiCom modifica los grosores nominales, que después se convertirán en el grosor del aglomerado, con los siguientes indicadores: 3,5 / 4,5 / 5,5 hasta 15,5. En nuestro ejemplo, se ha tomado un grosor de pared de diseño de 4,3 mm como referencia para los indicadores del grosor de aglomerado. El grosor de pared necesario será mayor, porque el indicador mecánico es menor. El grosor nominal seleccionado para el revestimiento sería de 4,5 mm. Queda claro así que no cambia nada en la propia elección del revestimiento.
Oportunidades y riesgos - Conclusión
Por una parte, la reformulación facilita la exactitud dimensional y la homogeneidad de los indicadores mecánicos para todo el sector. Las capas ricas en resina siguen formando parte del laminado para la mecánica real y para la determinación de los indicadores y ya no es necesario medirlas con procesos complicados para determinar el módulo E y la resistencia para después restarlas del cálculo. Pero, por otro lado, también supone un cambio de enfoque por parte de todos los participantes. Los fabricantes, sus clientes, los institutos de ensayos, los ingenieros de planificación y los operadores de red deben dominar esta vía. El objetivo es aportar transparencia y claridad al mercado.
Porque una cosa es segura: algunos indicadores específicos como, por ejemplo, el módulo E, se reducen con este cambio de la base de comprobación. Sin embargo, como la referencia geométrica en forma de grosor de pared es mayor, el indicador realmente relevante, la rigidez anular, no cambia.
El decir, que el rendimiento y la gran calidad de la manga no se ven afectados. Únicamente ha cambiado la forma en que se describen, no así la estructura real, la construcción o los materiales empleados.
SAERTEX® multiCom GmbH, como fabricante de entubado continuo de PRFV con curado UV, se rige por la normativa ISO aplicable. Por tanto, se van adaptando sucesivamente todos los fundamentos técnicos relevantes y se informa a los clientes con tiempo sobre los cambios resultantes.
Autor
Timo Münstermann M.Sc.
Gerente de producto
SAERTEX multiCom, Saerbeck
Tel: +49 2574 902-0
Gracias a 3R por facilitar el artículo.