Mediante una mejora en el proceso de fabricación, SAERTEX multiCom ha logrado reducir considerablemente las emisiones de CO2 y crear SAERTEX-LINER UPgreen, una manga de PRFV aún más sostenible.
El saneamiento de tuberías sin zanja contribuye enormemente, desde hace décadas, a proteger el medio ambiente. Mediante el diseño mejorado de la manga de PRFV, la larga vida útil de los productos y el uso de luz UV para el curado, hace tiempo que la capacidad innovadora del sector ha hecho realidad optimizaciones evidentes. SAERTEX multiCom presenta el nuevo SAERTEX-LINER UPgreen, una innovación enmarcada en esta tradición y que permite considerables ahorros de CO2. Mediante la mejora del proceso de producción de la resina, en un paso de la producción se genera un 45 % menos de emisiones que hasta ahora. Esta innovación es un primer paso afortunado hacia una orientación aún más sostenible de SAERTEX multiCom en el marco de la nueva estrategia de la empresa.
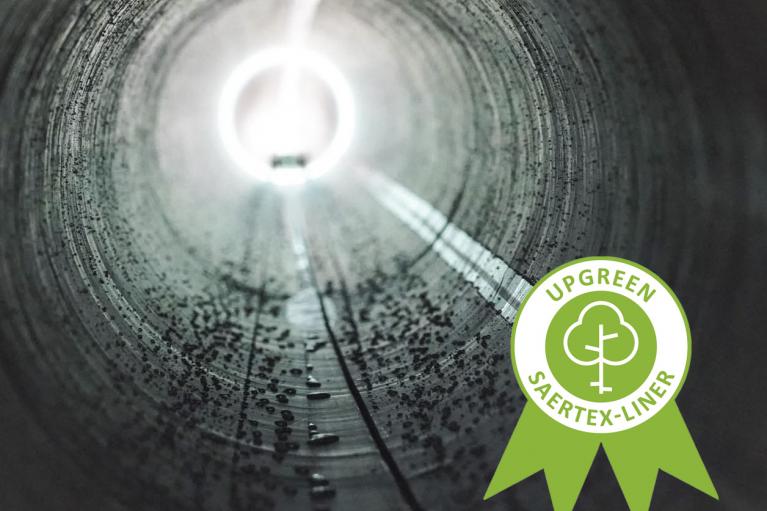
El año 2020 ha puesto patas arriba las principales preocupaciones del planeta. Lo que antes se discutía intensamente en todos los niveles de la sociedad, ha quedado casi olvidado debido a la pandemia. Pero el cambio climático sigue siendo un tema nuclear, de actualidad también por las masivas emisiones de CO2. El saneamiento de tuberías sin zanja per se contribuye enormemente, desde hace décadas, a proteger el medio ambiente. Además del propio saneamiento, que contribuye a reducir las emanaciones e infiltraciones en el canal, la tecnología sin zanja es más ecológica que la construcción abierta debido a la menor carga sonora y a la eliminación de las excavaciones. SAERTEX multiCom tiene la intención de incrementar esta contribución en el futuro. La innovación continua para una mayor sostenibilidad se ha definido como un componente esencial de la nueva estrategia empresarial. Pero SAERTEX multiCom ya ha trabajado en la última década en el tema de la sostenibilidad.
¿Por qué es sostenible ya hoy el saneamiento sin zanja de tuberías con mangas que se curan con luz?
La necesaria descarbonización ocupa el centro de atención de muchos sectores industriales. La opinión pública ya conoce este tema sobre el ejemplo de la electrificación de la industria del automóvil. Pero la industria de los revestimientos no se mantiene ajena a esta tendencia. ¿Qué se ha hecho en las últimas décadas?
1. Uso más eficiente del material gracias al diseño optimizado de las mangas de PRFV.
Sobre la base del desarrollo de SAERTEX-LINER se puede observar, por ejemplo, el enorme esfuerzo realizado para ahorrar materias primas, con seguridad, uno de los mayores motores de la reducción de las emisiones de CO2. SAERTEX-LINER del tipo S se instaló con éxito en todo el mundo hasta 2016, aproximadamente. Unos años antes se inició el desarrollo en SAERTEX multiCom con la optimización del diseño del revestimiento. El objetivo era mantener todas las propiedades positivas de este valorado producto, usar las mismas materias primas y, al mismo tiempo, elevar claramente los indicadores mecánicos.
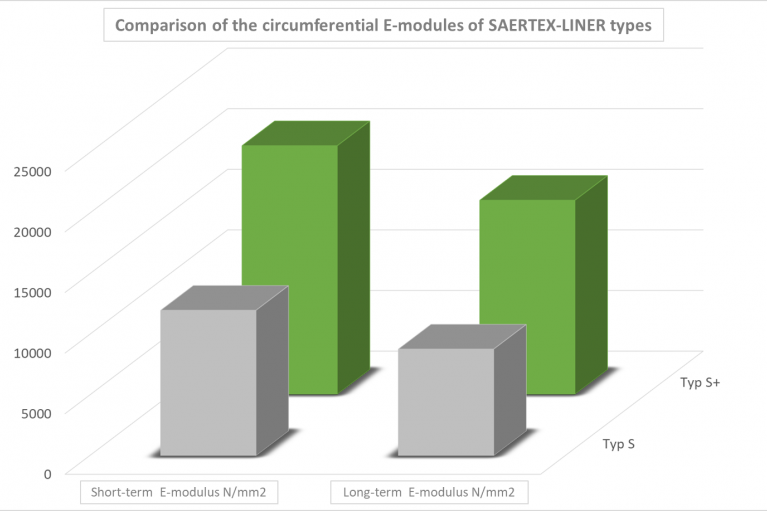
La clave del éxito era la experiencia y los conocimientos en técnicas de textil de todo el Grupo SAERTEX, líder en el mercado mundial de aplicaciones multiaxiales de fibra de vidrio. El resultado fue que prácticamente se duplicaron los indicadores mecánicos del nuevo revestimiento. La evolución al SAERTEX-LINER Tipo S+ tuvo como consecuencia la posibilidad de reducir enormemente los grosores de pared. Desde hace más de seis años, demostramos todos los días que la reducción del grosor de pared se consolidó con éxito y que no influye en la seguridad funcional y la vida útil técnica.
¿Qué influencia tuvo este desarrollo en la huella ecológica del producto? Se logró un claro ahorro de hasta el 25 % en las materias primas. Los menores grosores de pared, además, permitían una mayor velocidad de curado, con la consiguiente reducción evidente en el consumo de energía en la obra.
DN 400 | DN 1200 | |
Tipo S (MKG 18) | 4 mm | 10 mm |
Tipo S+ (MKG 25) | 3 mm | 8 mm |
Los grosores de pared compuestos que se deben pedir se basan en la norma DWA-M 144-3, con un nivel de agua básico de 3,5 m
2. Durabilidad técnica de hasta 100 años
¿Cuál es el revestimiento más sostenible? Es el revestimiento que se mantiene más tiempo en funcionamiento. Por tanto, todas las optimizaciones en todo el sistema se deben considerar siempre bajo el prisma de la durabilidad. Los cambios en las materias primas que provocaran una reducción de la vida útil serían contraproducentes. Por eso en SAERTEX multiCom solo se usan sistemas de resinas de gran calidad y fibras de vidrio con una excepcional resistencia a la corrosión. El equilibro óptimo entre todos los componentes se debe al departamento de desarrollo, que lleva décadas acumulando experiencia y conocimientos especializados. El sistema completo incluye, además del revestimiento, una tecnología de curado idónea para el producto. Para garantizarlo, se prueban prácticamente todos los tipos nuevos de instalaciones de UV y fuentes de luz con los revestimientos correspondientes en un complejo proceso de pruebas en la Llanura de Münster. Esto permite contar con una especificación muy delimitada y a medida para el curado del revestimiento correspondiente.
El siguiente componente es un instalador que entienda perfectamente el producto, la tecnología de curado y las especificaciones de instalación. Es la única forma de garantizar una elevada seguridad en el proyecto. SAERTEX multiCom se centra desde hace tiempo en un programa de formación integral y en el soporte técnico de los trabajadores sobre el terreno. Pero, fieles al lema «Detenerse es retroceder», seguiremos ampliando esta oferta en el futuro.
Al tratarse de un producto de construcción que endurece in situ, todavía faltan algunas piezas. Las siguientes son las pruebas secundarias de calidad en los productos montados y la necesaria planificación previa de cada instalación. Por todo el mundo se han fundado institutos de pruebas que han adquirido un conocimiento especializado sobre el revestimiento en mangas y su instalación. Sobre esta base, los institutos de pruebas han colaborado en las últimas décadas en el desarrollo de procesos de pruebas específicos para el revestimiento, pruebas de control de calidad para los productos instalados y un adecuado control externo de su fabricación, y ahora aplican estos desarrollos a diario. Los institutos contribuyen, con el control del sistema completo, que consta de la fabricación e instalación de la manga, a la sostenibilidad de esta tecnología aplicada con éxito en todo el mundo. Porque solo si la calidad es adecuada, se puede obtener una larga vida útil. SAERTEX multiCom se beneficia, desde hace más de 25 años, de la estrecha colaboración con los distintos institutos de pruebas. Los municipios y los estudios de ingeniería han aportado su conocimiento en la creación de reglamentos y elaboran a diario las bases para el éxito en la instalación.
La última pieza son las pruebas de tipo. Antes de poder lanzar un producto al mercado, se somete a un programa de pruebas muy complejo. Para el mercado alemán, esto suele desembocar en la denominada licencia general de obra / homologación general del modelo del DIBt, el Instituto Alemán de Tecnología de la Construcción. Este documento se reconoce en muchos países además de en Alemania pero, lamentablemente, no en todo el mundo, por lo que un fabricante de una manga de PRFV debe obtener muchas homologaciones nacionales distintas y superar las pruebas pertinentes. Para minimizar este esfuerzo, se trata de conseguir una armonización de los reglamentos. Actualmente se está dando un paso muy importante en este sentido, en el grupo de trabajo 6 del TC 13(/SC 8 a nivel de ISO. En este grupo de trabajo se está redactando la norma ISO 23818-2. Se trata de la «Valoración de la conformidad de los sistemas de tuberías de plástico para el saneamiento de tuberías existentes». La segunda parte mencionada tendrá validez para las mangas de PRFV.
¿Qué resultados se obtienen de estos ensayos de tipo? Los principales resultados son el cálculo de los valores mecánicos a corto y largo plazo, la resistencia a los productos químicos y la estabilidad operativa. Los valores a corto plazo derivados de los ensayos de tipo sirven como referencia para las pruebas de control de calidad de las muestras de obra. Si se cumplen o superan los valores específicos del revestimiento, la calidad empleada responde, desde el punto de vista mecánico, a lo que las partes implicadas desean y han acordado contractualmente. Mediante la certificación de las propiedades del producto instalado se puede tender un puente con los ensayos de tipo realizados. La calidad producida sobre el terreno responde a lo que se había determinado en el instituto de pruebas acreditado. De este modo, los valores mecánicos a largo plazo y las características de estabilidad operativa obtenidos en el laboratorio se pueden transferir a la manga de PRFV instalada. Para SAERTEX-LINER Tipo S+, por ejemplo, sobre la base de DIN EN 761 se obtuvo el factor de reducción 1,28 tras 10 000 horas y el factor de reducción 1,31 tras 20 000 horas. Estos valores tienen aplicación en el cálculo estático del revestimiento para 50 o 100 años. Pero, ¿es realista una vida útil de 100 años? Solo han pasado 50 años desde que Eric Wood inventara esta tecnología en 1971. En 2011 [1] se pudo observar, en revestimientos que llevaban 26 años instalados, que los productos seguían cumpliendo los requisitos de la norma ASTM F1216 al cabo de esta vida útil. Esta es la norma aplicable para los revestimientos de fieltro. Si consideramos que las mangas de PRFV actuales usan materiales de mucha mayor calidad y que todo el sistema ha evolucionado, una durabilidad técnica de 100 años no es una idea descabellada.

Durabilidad técnica de 100 años a través de 20 000 horas de aplicación DIN EN 761.
3. Eficiencia energética mediante el curado con luz UV
El paso del revestimiento del denominado estado M al estado I se consigue mediante la polimerización de la resina. Habitualmente, este proceso se denomina «curado» del revestimiento. Los dos estados mencionados están definidos en la norma DIN EN ISO 11296-4: M de «manufactured» (fabricado) e I de «installed» (instalado). El primero es un producto semielaborado, que se transporta hasta la obra en forma de manga flexible. El segundo es el producto final curado.
Para los revestimientos de manga, disponemos de los siguientes métodos típicos de curado:
- Mediante calor: agua caliente (revestimiento de fieltro), vapor de agua (manga de PRFV)
- Mediante radiación UV (manga de PRFV)
El curado con agua caliente se suele usar únicamente para revestimientos de fieltro. En la información de GSTT [2] se observa que este proceso presenta, con diferencia, el peor balance de CO2 en la obra. En el caso de las mangas de PRFV, antiguamente contábamos con dos métodos típicos de curado (vapor de agua y radiación UV). En los primeros días de la manga de PRFV, solo se contaba con el curado basado en el calor y en la reacción química por efecto de los peróxidos. Sin embargo, en los últimos 15 años se ha impuesto la tecnología UV. Hoy, este método, basado en la división de fotoiniciadores UV, goza prácticamente de exclusividad en las mangas de PRFV.
¿Cómo influye este aspecto en la huella ecológica? En la información de GSTT [2] observamos que la influencia es enorme. Se arrojan valores de CO2 para los distintos métodos de curado de las mangas de PRFV. La tecnología UV reduce el valor hasta en un 66 % en comparación con el curado por vapor.
Con el fin de ampliar aún más esta ventaja, SAERTEX multiCom se ha propuesto seguir optimizando el curado. Indudablemente, la tecnología UV optimizada es un componente esencial. Los distintos fabricantes han contribuido a este desarrollo.
Si, hace 15 años, solo se encontraban en el mercado cadenas de luminarias de 8x400 W y 4x100 W, ahora se emplean nuevas geometrías de las fuentes de luz, denominadas núcleos, además de lámparas de UV de mayor potencia. Esto se debe, por una parte, a que han aparecido mangas de PRFV con nuevas dimensiones - hasta DN 1600 y superiores - y se persigue la reducción de los tiempos de curado. Esta mejora en la eficiencia energética tiene un efecto positivo en los aspectos de rentabilidad y sostenibilidad del proceso.

Emisiones de CO2 de distintos procesos de curado para mangas
(F: Calculadora de CO2 para mangas de revestimiento, versión 2.2" en la figura 14 (2014))
La industria del revestimiento también ha estado activa en lo tocante a la optimización del curado. Así, SAERTEX multiCom cuenta con más de 20 años de colaboración con la escuela superior de Münster y la cátedra local de Química Macromolecular y Tecnología del Plástico. Su director, el prof. Lorenz es un científico puntero a escala mundial en el ámbito de las resinas de reacción, particularmente las resinas de polímeros insaturados (UP) y de éster de vinilo (VE). En múltiples trabajos de diplomatura, máster y doctorado se ha estudiado científicamente la optimización de los sistemas de resinas, particularmente para la aplicación en mangas de revestimiento de PRFV con telas multiaxiales.
Estos esfuerzos derivaron, entre otras cosas, en la patente de un «sistema iniciador altamente reactivo para revestimientos de curado UV», una tecnología de la que se benefician los clientes de SAERTEX multiCom a través de un claro aumento de la velocidad de curado y el ahorro del consumo de energía en la obra.
SAERTEX-LINER UPgreen – un primer paso para aumentar el ahorro de CO2 con UV-CIPP.
De este modo, se puede determinar que todas las partes participantes en el sistema han contribuido enormemente a la protección del medio ambiente y lo siguen haciendo a diario. Sobre la base del lema «El futuro es la consecuencia de nuestras decisiones de hoy», SAERTEX multiCom está convencida de que es necesario realizar nuevos esfuerzos, que nos llevarán a éxitos futuros en el desarrollo sostenible de la tecnología UV-CIPP.
Y ya podemos anunciar un primer hito en este sentido: el revestimiento SAERTEX-LINER UPgreen. Tras tomar la decisión, calificada de estratégica, de centrar la atención en el tema de la sostenibilidad, SAERTEX multiCom ha acudido a uno de sus socios estratégicos. A comienzos de 2020 se puso en marcha el proyecto de desarrollo bilateral «sustainability by UPgreen» con el especialista en sistemas de resina Scott Bader. El objetivo definido fue la drástica reducción de las emisiones de CO2 en toda la cadena de producción de la resina UP, al tiempo que se mantenía su composición química, las propiedades mecánicas y químicas y las materias primas empleadas. En resumen: la resina para el SAERTEX-LINER debía seguir siendo la misma.
Los cambios en la resina se pudieron ir descartando sistemáticamente en todo el desarrollo del proyecto, por lo que todas las homologaciones de SAERTEX-LINER mantienen su validez. Las emisiones de CO2 en un paso esencial de la producción de la resina se redujeron en un 45 % gracias a todo el trabajo de desarrollo. De este modo, solo en el último trimestre de 2020 se logró un ahorro de 270 000 kg de CO2 en 160 000 metros lineales SAERTEX-LINER vendidos con resina UP.
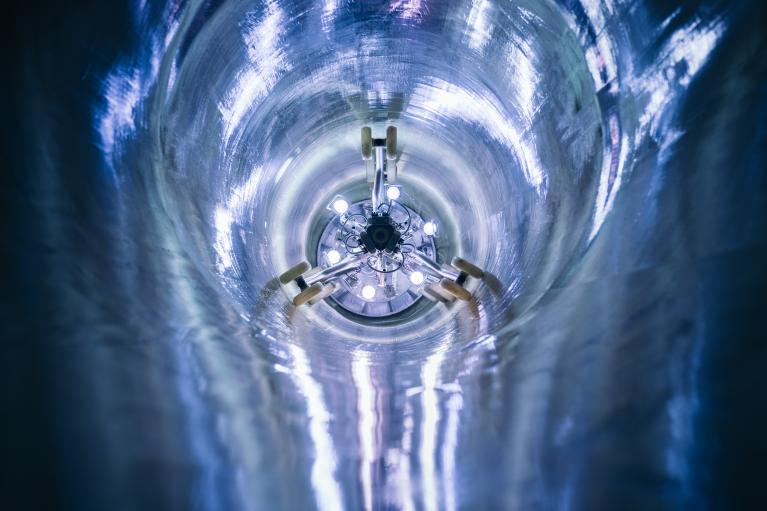
Eficiencia energética: Uso de luz UV en lugar de vapor de agua para curar el revestimiento
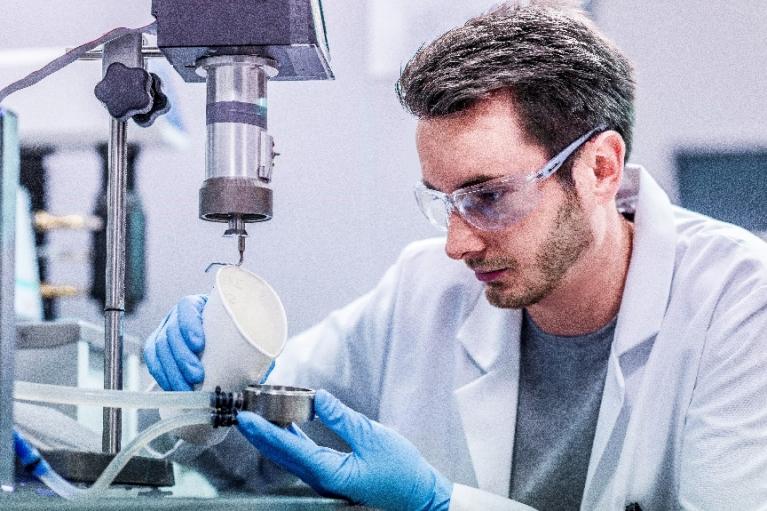
Ahorro del 45 % de CO2, valores técnicos constantes con SAERTEX-LINER UPgreen
Hasta ahora, SAERTEX multiCom solo ha introducido la tecnología UPgreen en Europa; China y EE. UU. le seguirán en un futuro. Con la nueva tecnología UPgreen, solo para Europa se obtiene un ahorro de CO2 calculado en más de un millón de kilogramos de CO2 en los próximos doce meses. Incluye todos los SAERTEX-LINER de la gama de productos con resinas UP. Estas mangas de PRFV se emplean predominantemente para el saneamiento sin zanja de canales de aguas residuales municipales con flujo por gravedad y en tuberías bajo presión. Además, esta resina se aplica en revestimientos para el saneamiento de conductos de gas. SAERTEX multiCom comunica trimestralmente a sus clientes los resultados demostrables conseguidos con UPgreen en la optimización de CO2. Para ello, se proporciona a los clientes un certificado con un cálculo individual del ahorro de CO2 para sus pedidos en ese periodo. Este certificado también sirve a los clientes para demostrar su contribución al ahorro de CO2. Ya se han enviado los primeros certificados.
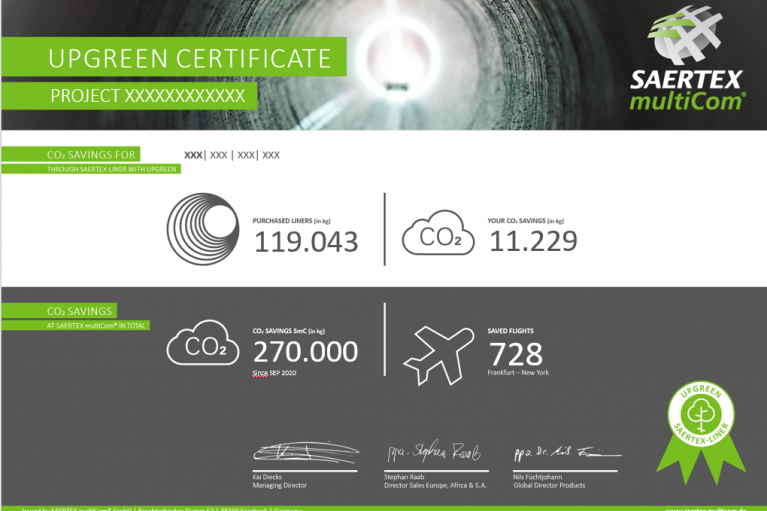
Certificado de SAERTEX-LINER® UPgreen – información trimestral y por proyectos de la reducción de CO2.
SAERTEX multiCom considera que este solo es un hito más en materia de sostenibilidad y seguirá trabajando intensamente sobre este tema. Se han definido equipos de proyecto que examinan con lupa otras materias primas, o bien trabajan sobre los procesos en SAERTEX multiCom.
¿Cuál es el auténtico grado de calidad de SAERTEX multiCom? Todavía no tenemos una respuesta concluyente para esta pregunta, pero la tendremos en un futuro. Para medir la sostenibilidad, se ha encargado a un instituto independiente la elaboración de una «huella de carbono» actualizada. Con ella podremos definir aún mejor las reducciones de 1 millón de kg de CO2 que persigue SAERTEX-LINER UPgreen. A modo de orientación: Esta reducción corresponde a unos 3000 vuelos de Fráncfort a Nueva York [3].
Agradecemos a B_I Medien su aportación.
QUELLEN