Grâce à une amélioration du processus de fabrication, SAERTEX multiCom réussit à réduire considérablement les émissions de CO2 et à rendre la gaine de tuyaux en PRV encore plus durable avec SAERTEX-LINER Upgreen.
Depuis des décennies, la réhabilitation des canalisations sans tranchée contribue énormément à la protection de l’environnement. Grâce à une conception améliorée des gaines de tuyaux en PRV, à la longue durée de vie des produits, ainsi qu’à l’utilisation de la lumière UV pour le durcissement, des optimisations importantes ont déjà été réalisées dans le passé grâce à la puissance d’innovation de l’industrie. Avec le nouveau SAERTEX-LINER UPgreen, SAERTEX multiCom présente une autre innovation qui s’inscrit dans cette tradition et permet des économies massives de CO2. L’amélioration du processus de fabrication de la résine permet de réduire de 45 % les émissions produites en une seule étape de production. Cette innovation est un premier pas réussi vers une orientation encore plus durable de SAERTEX multiCom, conformément à la nouvelle stratégie de l’entreprise.
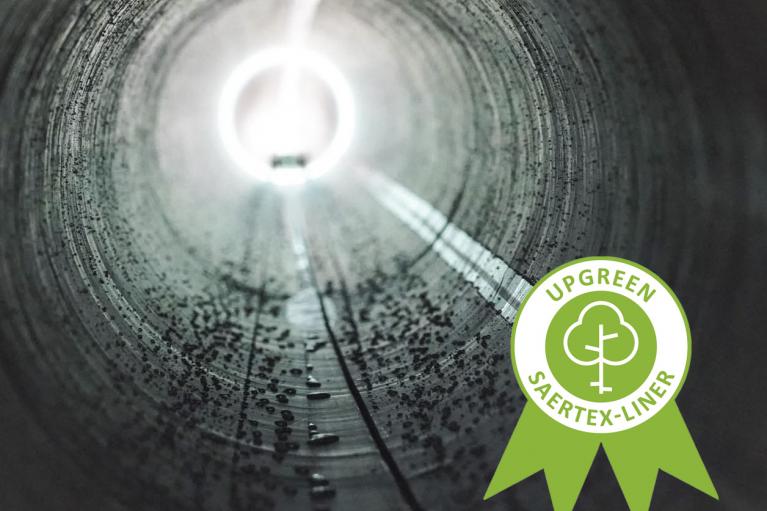
L’année 2020 a complètement bouleversé les priorités mondiales. Ce qui faisait auparavant l’objet d’intenses discussions à tous les niveaux de la société a été presque entièrement relégué au second plan en raison de la pandémie. Le changement climatique, dû aux émissions massives de CO2, reste toutefois l’une des questions centrales. Depuis des décennies, la réhabilitation des canalisations sans tranchée contribue énormément à la protection de l’environnement. Outre la réhabilitation proprement dite, qui contribue à réduire les infiltrations dans les égouts, la technologie sans tranchée est plus respectueuse du climat que la construction en tranchée ouverte en raison de la faible pollution sonore et de l’absence de travaux de terrassement. Cette contribution sera renforcée à l’avenir grâce à SAERTEX multiCom. L’innovation continue pour plus de durabilité a été définie comme un élément essentiel de la nouvelle stratégie d’entreprise. Cependant, SAERTEX multiCom a déjà abordé la question de la durabilité au cours de la dernière décennie.
Qu’est-ce qui rend durable dès aujourd’hui la réhabilitation sans tranchée des canalisations avec des gaines photopolymérisables ?
La nécessité de décarbonisation est au centre des préoccupations de nombreuses industries. Le grand public le connaît probablement par l’exemple de l’électromobilité dans l’industrie automobile. Mais l’industrie des gaines n’a pas non plus été impassible face à cette tendance. Qu’est-ce qui a été fait au cours des dernières décennies ?
1. Utilisation efficace des matériaux grâce à la conception optimisée de la gaine de tuyau en PRV.
La poursuite du développement du SAERTEX-LINER est un exemple des énormes efforts qui ont été faits pour économiser les matières premières, certainement l’un des plus grands leviers pour réduire les émissions de CO2. Le SAERTEX-LINER modèle S a été installé avec succès dans le monde entier jusqu’en 2016 environ. Quelques années plus tôt, le développement chez SAERTEX multiCom a commencé par l’optimisation du design de la gaine. L’objectif était de conserver toutes les propriétés positives du produit éprouvé, d’utiliser les mêmes matières premières et, en même temps, d’augmenter considérablement les valeurs caractéristiques mécaniques.
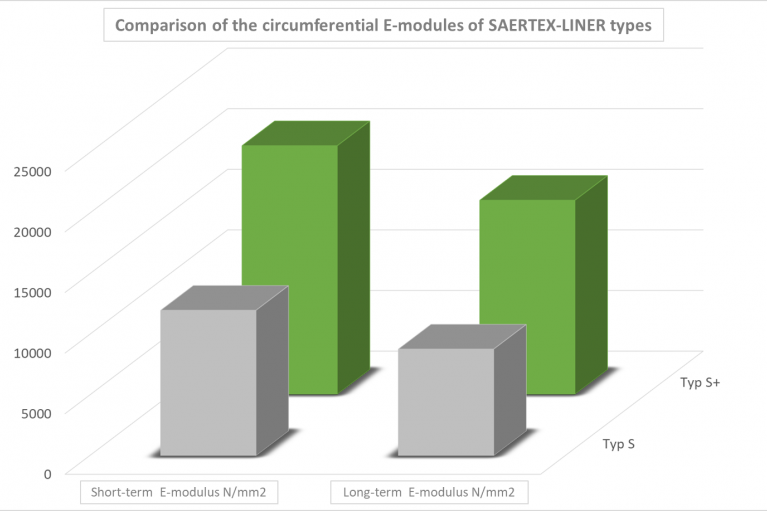
La clé du succès a été le savoir-faire technique en matière de textile de l’ensemble du groupe SAERTEX, leader mondial du marché des tissus multiaxiaux en fibres de verre. Le résultat a été un quasi-doublement des valeurs caractéristiques mécaniques de la nouvelle gaine. L’évolution vers le LINER-SAERTEX de modèle S+ a permis de réduire considérablement l’épaisseur des parois. Pendant plus de six ans, il a été prouvé quotidiennement que la réduction de l’épaisseur de la paroi pouvait être réalisée avec succès et que cela n’avait aucune influence sur la sécurité opérationnelle et la durée de vie technique.
Quelle influence cette évolution a-t-elle eue sur l’empreinte écologique du produit ? Une économie importante de matières premières, jusqu’à 25 %, a été possible. Les épaisseurs de paroi plus faibles peuvent également être traitées à une vitesse de passage plus élevée, ce qui se traduit par une consommation d’énergie nettement inférieure sur le chantier.
DN 400 | DN 1200 | |
Modèle S (MKG 18) | 4 mm | 10 mm |
Modèle S+ (MKG 25) | 3 mm | 8 mm |
Épaisseur de la paroi composite à commander en fonction de la DWA-M 144-3 à un niveau d’eau souterraine de 3,5 m
2. Durée de vie technique jusqu’à 100 ans
Quel est la gaine la plus durable ? C’est la gaine qui reste le plus longtemps en fonctionnement. Toutes les optimisations de l’ensemble du système doivent donc toujours être considérées en termes de longévité. Des modifications des matières premières qui entraîneraient une réduction de la durée de vie seraient contre-productives. Pour cette raison, seuls des systèmes de résine de haute qualité et des fibres de verre avec une résistance à la corrosion particulièrement élevée sont utilisés dans SAERTEX multiCom. Le service de développement est responsable de la coordination optimale des différents composants, qui a accumulé le savoir-faire correspondant au fil des décennies. Outre la gaine, le système global comprend également une technologie de durcissement adaptée de manière optimale au produit. Pour s’en assurer, presque tous les nouveaux types de systèmes UV et de sources lumineuses sont testés avec les gaines correspondantes dans le cadre d’une procédure d’essai élaborée à Münsterland. Il est ainsi possible de fournir une spécification personnalisée et très étroitement définie pour le durcissement de la gaine.
L’autre élément important est un utilisateur qui comprend parfaitement le produit, la technologie de polymérisation et les spécifications d’installation. C’est le seul moyen de garantir un niveau élevé de fiabilité du projet. Dans le passé, SAERTEX multiCom a déjà attaché une grande importance à un vaste programme de formation et à un soutien technique des ouvriers sur place. Mais fidèle à la devise : le statu quo est une régression, c’est pourquoi cette offre sera considérablement élargie à l’avenir.
Comme il s’agit d’un produit de construction à durcissement sur place, il manque encore d’autres éléments constitutifs. Viennent ensuite les essais d’accompagnement de la qualité des produits installés et la planification préalable nécessaire de chaque installation individuelle. Des instituts d’essai ont été créés dans le monde entier et ont acquis des connaissances très pointues sur les gaines de canalisations et leur installation. Sur cette base, les instituts d’essai ont contribué, au cours des dernières décennies, à l’élaboration de procédures d’essai spécifiques aux gaines, d’essais de contrôle de la qualité des produits installés et d’un contrôle externe approprié pour leur fabrication, qui sont désormais utilisés quotidiennement. En surveillant l’ensemble du système, c’est-à-dire la production et l’installation des gaines, les instituts contribuent ainsi à la durabilité de cette technologie, qui est utilisée avec succès dans le monde entier. La qualité est en effet le gage d’une longue durée de vie technique. Depuis plus de 25 ans, SAERTEX multiCom profite de l’étroite collaboration avec les différents instituts de contrôle. Les municipalités et les bureaux d’études ont apporté leurs connaissances à la création des réglementations et élaborent quotidiennement les conditions nécessaires à des installations réussies.
Le dernier élément est constitué par les essais de type. Avant qu’un produit puisse être lancé sur le marché, il est soumis à un programme d’essais très élaboré. Pour le marché allemand, cela se traduit généralement par un agrément général/une homologation générale de la part du DIBt, l’Institut allemand de la technologie de la construction. Ce document est reconnu dans plusieurs autres pays que l’Allemagne, mais malheureusement pas au niveau mondial, de sorte qu’un fabricant de gaines en PRV doit faire face à de nombreuses approbations spécifiques à chaque pays et aux essais associés. Afin de réduire ces charges de travail, une harmonisation mondiale des réglementations est souhaitable. Un pas très important dans cette direction est actuellement franchi au sein du groupe de travail 6 du comité technique 138/SC 8 au niveau de l’ISO. Dans ce groupe de travail, la norme ISO 23818-2 est en cours de rédaction. Il s’agit de « l’évaluation de la conformité des systèmes de canalisations en plastique pour la réhabilitation des canalisations existantes ». La deuxième partie mentionnée sera valable pour les gaines de tuyaux en PRV.
Quels sont les résultats obtenus à partir de ces essais de type ? La détermination des valeurs mécaniques à court et à long terme, la résistance chimique et la stabilité opérationnelle sont au premier plan. Les valeurs à court terme des essais de type servent de valeurs de référence pour les essais de contrôle de la qualité des échantillons de chantier. Si les valeurs spécifiques à la gaine sont atteintes ou dépassées, la qualité installée d’un point de vue mécanique correspond à ce que toutes les parties impliquées visaient et avaient préalablement convenu par contrat. En prouvant les propriétés du produit installé, il est possible d’établir un lien avec les essais de type qui ont été réalisés. La qualité produite sur place correspond à ce qui a été déterminé dans l’institut d’essai accrédité. Ainsi, les valeurs mécaniques à long terme et les caractéristiques de la résistance opérationnelle déterminées à l’échelle du laboratoire peuvent être transférées à la gaine tubulaire en PRV installée. Pour le AERTEX-LINER de modèle S+, par exemple, le facteur de réduction 1,28 a été déterminé après 10 000 heures et le facteur de réduction 1,31 après 20 000 heures conformément à la norme DIN EN 761. Ces valeurs sont utilisées dans le calcul statique de la gaine pour 50 ans ou 100 ans Mais une telle durée de vie de 100 ans est-elle réaliste ? 50 ans se sont écoulés depuis qu’Eric Wood a inventé cette technologie en 1971. Dès 2011 [1], il a été démontré, sur la base de gaines installées depuis 26 ans, que les produits dépassent encore largement les exigences de la norme ASTM F1216, même après cette durée de vie. Cette norme est la norme définitive pour les gaines en feutre. Si l’on considère que les gaines en PRV d’aujourd’hui utilisent des matières premières de qualité nettement supérieure et que l’ensemble du système a été perfectionné, une durée de vie technique de 100 ans n’est pas un vœu pieux.

Durée de vie technique de 100 ans par 20 000 heures selon la norme DIN EN 761.
3. Efficacité énergétique grâce au durcissement par la lumière UV
Le transfert du revêtement de l’état M à l’état I s’effectue par la polymérisation de la résine. Ce processus est généralement appelé « durcissement » de la gaine. Les deux états mentionnés sont définis dans la norme DIN EN ISO 11296-4 : M pour « manufactured » (fabriqué) et I pour « installé ». Le premier est le pré-produit, qui est transporté sur le chantier sous la forme d’un tube souple et flexible. Le dernier est le produit final durci.
Les méthodes de durcissement suivantes sont généralement utilisées pour les gaines tubulaires :
- Par la chaleur : eau chaude (gaine en feutre), vapeur (gaine en PRV).
- Par le biais des rayons UV (gaine tubulaire en PRV)
La polymérisation à l’eau chaude n’est généralement utilisée que pour les gaines en feutre. Les informations du GSTT [2] montrent que cette méthode présente de loin le pire bilan carbone sur le chantier. Dans le passé, il existait généralement deux méthodes de polymérisation pour les gaines de canalisations en PRV (vapeur et rayonnement UV). Au début de l’histoire des gaines en PRV, il n’existait qu’un durcissement basé sur la chaleur et reposant sur l’effet des peroxydes dans la réaction chimique. Cependant, au cours des 15 dernières années, cette technologie a été de plus en plus remplacée par la technologie UV. Aujourd’hui, cette méthode, qui repose sur la scission des photo-initiateurs par le rayonnement UV, occupe une position quasi monopolistique dans le domaine des gaines en PRV.
Comment cet aspect influe-t-il sur l’empreinte écologique ? Les informations du GSTT [2] montrent que l’influence est énorme. Les chiffres de CO2 pour les différentes méthodes de durcissement des gaines en PRV sont indiquées. La technologie UV permet d’obtenir des valeurs jusqu’à 66 % inférieures à celles du durcissement à la vapeur.
Afin d’accroître cet avantage, SAERTEX multiCom a entrepris d’optimiser davantage le processus de durcissement. L’optimisation de la technologie UV en est sans aucun doute un élément important. Les différents fabricants ont apporté leur contribution.
Alors qu’il y a 15 ans, seules les chaînes lumineuses de 8x400 W et 4x1000 W étaient courantes sur le marché, de nouvelles géométries de sources lumineuses, que l’on appelle des noyaux, ainsi que des lampes UV à plus haut rendement se sont imposées entre-temps. Cela s’explique d’une part par le fait que les gaines en PRV ont atteint de nouvelles dimensions - jusqu’à DN 1600 et au-delà - et que des temps de durcissement plus courts ont été recherchés. Cette meilleure efficacité énergétique a un impact positif sur les aspects économiques et de durabilité du processus.

Émissions de CO2 de différentes méthodes de durcissement des gaines de tuyaux
(S : Le calculateur de CO2 pour le gainage des tuyaux version 2.2" est la figure 14 (2014)).
L’industrie de la gaine elle-même s’est penchée aussi sur la question de l’optimisation du durcissement. Ainsi, SAERTEX multiCom peut se prévaloir de plus de 20 ans de coopération avec l’Université des sciences appliquées de Münster et sa chaire de chimie macromoléculaire et de technologie des matières plastiques. Son directeur, le professeur Lorenz, est l’un des plus grands scientifiques au monde dans le domaine des résines réactives, notamment les résines UP et VE. Dans de nombreuses thèses de licence, de master et de doctorat, l’optimisation des systèmes de résine, en particulier pour l’application dans les gaines de tuyau en PRV avec des couches multiaxiales, a été étudiée scientifiquement.
Ces efforts ont abouti, entre autres, au brevetage d’un « système d’initiateur hautement réactif pour les gaines avec polymérisation à la lumière UV », une technologie dont les clients de SAERTEX multiCom bénéficient grâce à une augmentation significative de la vitesse de production et donc aussi à une économie de la consommation d’énergie nécessaire sur le chantier.
SAERTEX-LINER UPgreen - un premier pas vers de nouvelles économies de CO2 avec UV-CIPP
On peut donc affirmer que toutes les parties impliquées dans le système ont apporté et continuent d’apporter une contribution massive à la protection de l’environnement au quotidien. Sur la base de la devise « L’avenir est la conséquence de nos décisions d’aujourd’hui », SAERTEX multiCom est convaincu que des efforts supplémentaires sont nécessaires et que des succès futurs sont possibles dans le développement durable de la technologie UV-CIPP.
Et un premier jalon sur cette voie peut désormais être dévoilé : le SAERTEX-LINER Upgreen. Après avoir pris la décision stratégique de se concentrer sur la durabilité, SAERTEX multiCom a contacté l’un de ses partenaires stratégiques. Début 2020, le projet de développement bilatéral « sustainability by UPgreen » a été lancé avec le spécialiste des systèmes de résine Scott Bader. L’objectif a été défini comme la réduction radicale des émissions de CO2 tout au long de la chaîne de production de la résine UP, tout en maintenant la composition chimique, les propriétés mécaniques et chimiques et les matières premières utilisées. En résumé : la résine pour le SAERTEX-LINER devait rester identique.
Les modifications de la résine ont pu être systématiquement exclues tout au long du projet, ce qui signifie que toutes les approbations existantes du SAERTEX-LINER restent valables. Les émissions de CO2 d’une étape clé de la fabrication de la résine ont été réduites de 45 % grâce au travail de développement conjoint. Ainsi, rien qu’au dernier trimestre de 2020, 270 000 kg de CO2 ont déjà été économisés sur les 160 000 mètres courants de SAERTEX-LINER avec résine UP vendus.
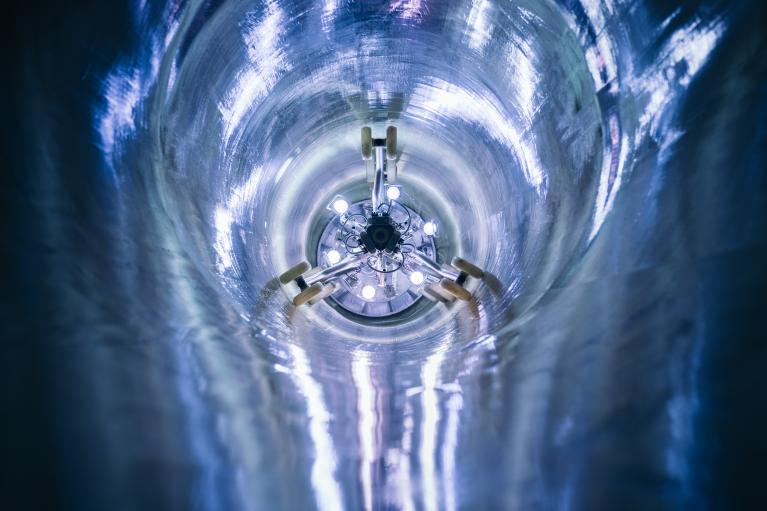
Efficacité énergétique : Utilisation de la lumière UV au lieu de la vapeur pour le durcissement des gaines.
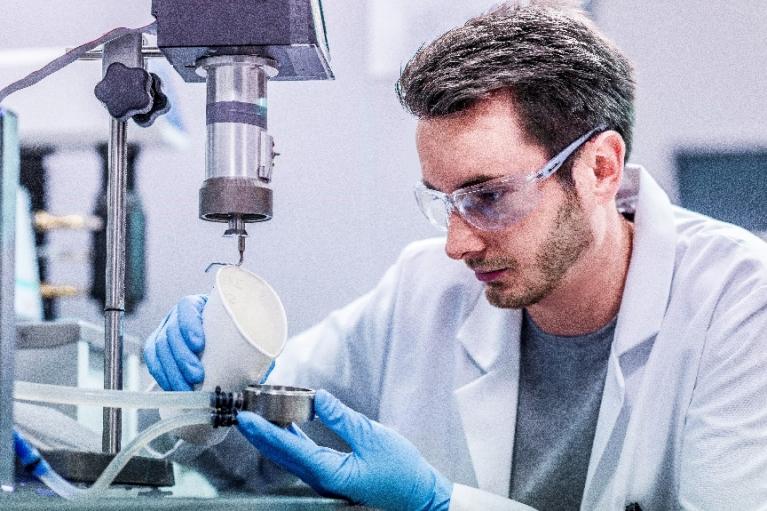
Économie de CO2 de 45 %, valeurs techniques constantes avec le SAERTEX-LINER Upgreen.
Jusqu’à présent, SAERTEX multiCom n’a introduit la technologie UPgreen qu’en Europe ; la Chine et les États-Unis suivront prochainement. La nouvelle technologie UPgreen permet de calculer une économie de plus d’un million de kilogrammes de CO2 au cours des douze prochains mois pour la seule Europe. Il comprend toutes les SAERTEX-LINER de la gamme de produits avec des résines UP. Ces gaines en PRV sont principalement utilisées pour la réhabilitation sans tranchée des canalisations municipales d’eaux usées à écoulement gravitaire ou sous pression. En outre, cette résine est utilisée dans les gaines pour la réhabilitation des gazoducs. Chaque trimestre, SAERTEX multiCom transmet à ses clients les résultats vérifiables de l’optimisation des émissions de CO2 obtenus grâce à Upgreen. En retour, les clients reçoivent un certificat avec un calcul personnalisé des économies de CO2 pour leurs commandes pendant cette période. Avec ce certificat, les clients peuvent également attester leur part d’économie de CO2. Les premiers certificats ont déjà été envoyés.
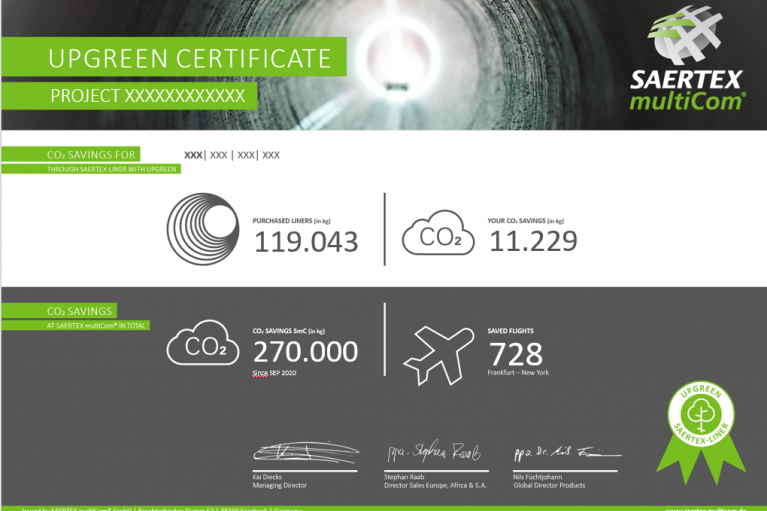
Certificat UPgreen SAERTEX-LINER® – informations trimestrielles et par projet sur les économies de CO2.
SAERTEX multiCom considère qu’il s’agit d’une étape supplémentaire en matière de durabilité et continuera à travailler intensivement sur ce thème. Des équipes de projet ont été définies pour étudier de plus près d’autres matières premières ou pour examiner les processus chez SAERTEX multiCom.
Quelle est la qualité réelle de SAERTEX multiCom ? Cette question n’a pas encore reçu de réponse concluante, mais ce sera le cas à l’avenir. Pour s’assurer que la durabilité est mesurable, une « empreinte carbone » actualisée a été commandée à un institut indépendant. Les économies d’un million de kg de CO2 visées par le SAERTEX-LINER UPgreen pourront ainsi être mieux classées. À titre de comparaison, cette économie correspond à près de 3 000 vols de Francfort à New York [3].
Merci à B_I Medien pour la mise à disposition de l’article.
[1] E. Allouche, S. Alam, R. Sterling, W. Condit, A. Selvakumar; Forensic investigation of a generation old CIPP Liner; Paper D-5-04; NASTT No-Dig Show 2011
[2] GSTT Information Nr. 27 „CO2 Kalkulator für Schlauchrelining-Version 2.2“ Abbildung 14
[3] ICAO Carbon Emissions Calculator, pro Passagier, Economy Class