By improving the manufacturing process, SAERTEX multiCom has succeeded in significantly reducing CO2 emissions and making GRP pipe lining even more sustainable with the SAERTEX-LINER UPgreen.
Trenchless pipe rehabilitation has been contributing enormously to the protection of the environment for decades. An improved GRP pipe liner design, long product service life and the use of UV light for curing have already enabled significant optimizations to be achieved in the past thanks to the innovative strength of the industry. With the new SAERTEX-LINER UPgreen, SAERTEX multiCom presents yet another innovation that follows in this tradition and enables massive CO2 savings. Improvements in the resin manufacturing process have resulted in a production step that produces 45% less emissions than before. This innovation is a first, successful step towards an even more sustainable orientation of SAERTEX multiCom in line with the company's new strategy.
The year 2020 has completely disrupted the global focus. What had previously been discussed intensively at all corporate levels has almost completely been sidelined by the pandemic issue. One of the central issues continues to be climate change, however, which is also driven by massive CO2 emissions. Trenchless pipe rehabilitation per se has been contributing enormously to protecting the environment for decades. In addition to the rehabilitation itself, which helps reduce exfiltration and infiltration in the sewer, trenchless technology is more climate-friendly compared to the open trench method due to its low noise pollution and avoidance of open-trench construction. SAERTEX multiCom intends to further increase this contribution in future. Continuous innovation for more sustainability was defined as an essential component of the new corporate strategy. But SAERTEX multiCom has already addressed the issue of sustainability in the preceding decade.
What makes the trenchless rehabilitation of pipelines with light-curing pipe liners sustainable already today?
Many industries are focusing on the need for decarbonization. This is probably known to the general public through the example of electromobilization in the automotive industry. But this trend has not been ignored by the liner industry either. What has been done in recent decades?
1. Efficient Use of Materials Thanks to Optimized GRP Pipe Liner Design
The further development of the SAERTEX-LINER provides an example of the enormous efforts that have been made to save raw materials - certainly one of the greatest levers - in order to reduce CO2 emissions. The SAERTEX-LINER type S had been successfully installed worldwide until about 2016. A few years previously, SAERTEX multiCom started the development process by optimizing the liner design. The goal was to retain all the positive properties of the proven product while using identical raw materials while at the same time significantly increasing the mechanical characteristics.
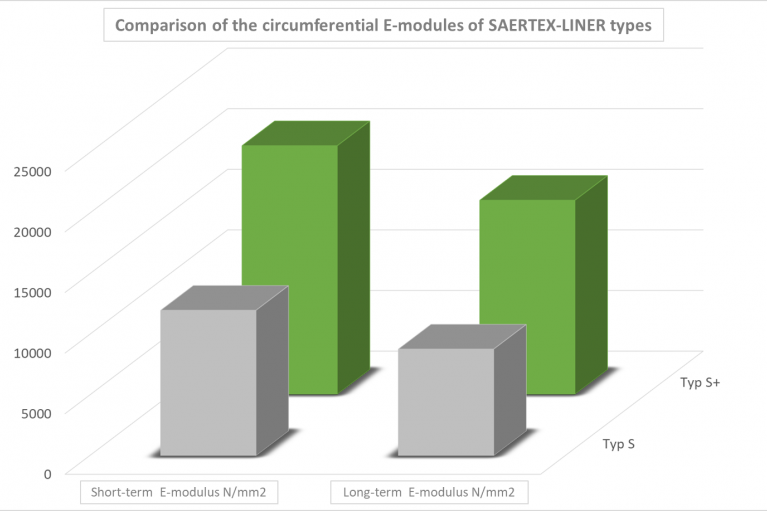
The key to success was the textile-related expertise of the entire SAERTEX Group, world market leader for multiaxial fabrics made of glass fibers. The result was almost a doubling of the mechanical characteristics of the new liner. The further developed SAERTEX-LINER type S+ resulted in a significant reduction of the wall thicknesses. Daily evidence, that has mounted over a period of more than six years, suggests that the wall thickness reduction has become successfully established without any impact on operational safety or technical service life.
How did this development affect the ecological footprint of the product? A significant saving in raw materials of up to 25% was possible. Thinner wall thicknesses can also be cured at a higher pull-through speed, which is associated with noticeably lower energy consumption on the construction site.
DN 400 | DN 1200 | |
Type S (MKG 18) | 4 mm | 10 mm |
Type S+ (MKG 25) | 3 mm | 8 mm |
Composite wall thickness em to be ordered based on DWA-M 144-3 at a groundwater level of 3.5 m
2. Technical Service Life of up to 100 Years
What is the most sustainable liner? It is the liner that has been operating fully functionally for the longest time. All optimizations to the entire system must therefore always be considered with a view towards longevity. Changes to raw materials which would lead to a reduction in service life would be counterproductive. This is why SAERTEX multiCom per se only uses high-quality resin systems and glass fibers with particularly high corrosion resistance. The optimum coordination of the individual components is the responsibility of the development department, which has built up appropriate know-how over the decades. In addition to the liner, the overall system also includes a curing technology that is optimally matched to the product. All new types of UV systems and light sources are tested with the respective liners in a complex test procedure in the Münsterland Region to ensure this. With this method, it is possible to provide a customized and very narrowly defined specification for the curing of the respective liner.
The next component is a user who perfectly understands the product, the curing technology and the specifications for installation. This is the only way to ensure a high level of project safety. SAERTEX multiCom has historically placed great emphasis on a close-knit training program and on-site technical support for its columns. But true to the adage, "stagnation means regression", this offer will be significantly expanded in future.
Since the product is a construction product that cures on site, there are additional components that are still missing. The next components are quality control tests on the installed products and the necessary pre-planning of each installation. Testing institutes have been established worldwide that have acquired very specialized knowledge about pipe liners and their installation. Over the past decades, these testing institutes have helped develop liner-specific test methods, quality monitoring tests for the installed products and suitable external monitoring for their manufacture, and these tests are now used on a daily basis. By monitoring the entire system, consisting of pipe liner production and installation, these institutes contribute to the sustainability of this technology that is successfully used worldwide. After all, a long technical service life is only possible if the quality is right. SAERTEX multiCom has been benefiting from close cooperation with the various testing institutes for more than 25 years now. The municipalities and engineering offices have incorporated their knowledge in the development of regulations and are working out the basics for successful installation on a daily basis.
Type tests represent the last component. Before a product can be launched on the market, it undergoes a very elaborate testing program. For the German market, the process usually culminates in a so-called general technical approval/general design approval from the DIBt, the German Institute for Construction Technology. This document is also recognized in several other countries besides Germany, but unfortunately not globally, so a manufacturer of a GRP pipe liner is faced with many different country-specific approvals and associated tests. The aim is to achieve global harmonization of the regulations in order to minimize this effort. A very important step in this direction is currently being taken in WG 6 of TC 138/SC 8 at the ISO level. The ISO 23818-2 standard is being written in this working group. This involves the "Conformity assessment of plastic pipeline systems for the rehabilitation of existing pipelines". The stated second part will apply to GRP pipe liners.
What results are obtained from these type tests? The emphasis is on determining the mechanical short-term and long-term values, chemical resistance and operational strength. The short-term values from the type tests serve as reference values for the quality-monitoring tests of the construction site specimens. If the liner-specific values are met or exceeded, the installed quality from a mechanical point of view corresponds to what all parties involved aimed for and previously contractually agreed. By proving the properties of the installed product, a link can be forged to the type tests that have been carried out. The quality produced on site corresponds to what was determined in the accredited testing institute. The long-term mechanical values and characteristics of the fatigue strength determined on a laboratory scale can thus be transferred to the installed GRP pipe liner. For the SAERTEX-LINER Type S+, for example, the reduction factor 1.28 was determined after 10,000 hours and the reduction factor 1.31 after 20,000 hours in accordance with DIN EN 761. The values are used in the static calculation of the liner for either 50 years or 100 years. But is such a long service life of 100 years realistic at all? It has now been 50 years since Eric Wood invented this technology in 1971. As early as 2011 [1], liners that had been installed for 26 years demonstrated that the products still far exceeded the requirements of the ASTM F1216 standard even after this service life. This is the definitive standard for felt liners. If one then considers that today's GRP pipe liners use raw materials of significantly higher quality and that the entire system has undergone further development, a technical service life of 100 years is not wishful thinking.
Technical service life of 100 years: 20,000-hour test based on DIN EN 761 | Graphic: IMA Dresden
3. Energy Efficiency through Curing with UV Light
The transformation of the liner from the so-called M-state to the I-state is achieved by polymerizing the resin. This process is usually called "curing" of the liner. The two states mentioned are defined in DIN EN ISO 11296-4: M is for "manufactured" and I is for "installed." The first is the preliminary product, which is transported to the construction site as a soft flexible tube. The latter is the cured end product.
Pipe liners typically have the following curing methods:
- By means of heat:: Hot water (felt liner) / Steam (GRP pipe liner)
- By means of UV radiation (GRP pipe liner)
Hot water curing is typically performed only for felt liners. The GSTT information [2] shows that this method has by far the worst CO2 footprint on the construction site. There were typically two curing methods for GRP pipe liners in the past (steam and UV radiation). During the early days of GRP pipe liner history, curing was only based on heat and reliance on the effect of peroxides in the chemical reaction. In the last 15 years, however, this has been increasingly superseded by UV technology. This method, which is based on the splitting of photoinitiators by UV radiation, now occupies a virtually exclusive position in the field of GRP pipe liners.
How does this aspect impact the ecological footprint? The GSTT information [2] indicates that the impact is enormous. It shows the CO2 values for the different curing methods for GRP pipe liners. Compared with steam curing, UV technology achieves a value that is up to 66% lower.
To further increase this advantage, SAERTEX multiCom has set itself the goal of further optimizing curing. An important part of this is undoubtedly the optimized UV technology. Various manufacturers have already contributed here.
15 years ago, only 8x400 W and 4x1000 W light chains were common on the market, but new light source geometries, so-called cores and also UV lamps with higher outputs have become established in the meantime. This was due, on the one hand, to the fact that GRP pipe liners have advanced into new dimensions - up to DN 1600 and beyond - and that shorter curing times were being sought. This improved energy efficiency pays positive dividends on the economic and sustainability aspects of the process.
CO2 emissions of different curing methods for pipe liners [2].
(CO2 calculator for pipe relining Version 2.2" Figure 14 (2014))
The liner industry itself has also been active on the issue of curing optimization. For example, SAERTEX multiCom can look back on more than 20 years of cooperation with the Münster University of Applied Sciences and its Chair of Macromolecular Chemistry and Plastics Technology. Its head, Prof. Lorenz, is one of the world's leading scientists in the field of reactive resins, especially UP and VE resins. Numerous diploma, master's and doctoral theses have scientifically investigated the optimization of resin systems specifically for use in GRP pipe liners with multiaxial fabrics.
These efforts resulted, among other things, in the patenting of a "highly reactive initiator system for UV light-curing liners," a technology that benefits SAERTEX multiCom customers by significantly increasing pull-through speed, thereby also achieving savings in the amount of energy consumed on the construction site.
SAERTEX-LINER UPgreen – A first step towards further CO2 savings with UV-CIPP.
We can thus state that all parties involved in the system have made – and continue to make – a massive contribution to environmental protection on a daily basis. Following the motto "The future is the consequence of the decisions we make today," SAERTEX multiCom is convinced that further efforts are necessary and that future successes are possible in the sustainable development of UV-CIPP technology.
And a first milestone in this direction can now be published: the SAERTEX-LINER UPgreen. After the previously mentioned strategic decision was made to focus on sustainability, SAERTEX multiCom approached one of its strategic partners. In early 2020, the bilateral development project "sustainability by UPgreen" was launched with resin systems specialist Scott Bader. The goal was defined as drastically reducing CO2 emissions throughout the UP resin production chain, while maintaining the chemical composition, mechanical and chemical properties, and raw materials used. In summary: the resin for the SAERTEX-LINER had to remain identical.
Changes in the resin could be systematically excluded throughout the project, which means that all existing approvals of the SAERTEX-LINER remain valid. CO2 emissions from a key production step in the manufacture of the resin were reduced by 45% as a result of the joint development work. In the last quarter of 2020 alone, 270,000 kg of CO2 were saved from 160,000 running meters of SAERTEX-LINER with UP resin that were sold.
So far, SAERTEX multiCom has launched the UPgreen technology only in Europe. China and the USA are to follow in future. With the new UPgreen technology, CO2 savings of over one million kilograms of CO2 are calculated for Europe alone over the next twelve months. It includes all SAERTEX-LINERs of the product range with UP resins. These GRP pipe liners are mainly used for trenchless rehabilitation of municipal sewers in the gravity range and pipelines in the pressure range. This resin is also used in liners for the rehabilitation of gas pipelines.
SAERTEX multiCom passes on the demonstrable results in CO2 optimization from UPgreen to its customers each quarter. Customers receive a certificate for this purpose with an individual calculation of the CO2 savings for their orders in that time period. Customers can also substantiate their part of the CO2 savings with this certificate. The first certificates have already been sent out.
SAERTEX-LINER UPgreen certificate – quarterly and project-related information on CO2 savings
SAERTEX multiCom considers this to be just another milestone on the subject of sustainability and will continue to work intensively on this topic. Project teams have been defined to examine other raw materials or to look into the processes at SAERTEX multiCom.
How good is SAERTEX multiCom really? This question has not yet been conclusively settled, but should also be answered in the future. To ensure that sustainability is measurable, the creation of an updated "carbon footprint" has been commissioned from an independent institute. It will then be possible to better classify the savings of 1 million kg CO2 targeted by the SAERTEX-LINER UPgreen. But to give you a guideline at this stage: This saving corresponds to almost 3,000 flights from Frankfurt to New York [3].
Thanks to B_I Medien for making the contribution available.
[1] E. Allouche, S. Alam, R. Sterling, W. Condit, A. Selvakumar; Forensic investigation of a generation old CIPP Liner; Paper D-5-04; NASTT No-Dig Show 2011
[2] GSTT information No. 27 "CO2 calculator for pipe relining Version 2.2" Figure 14
[3] ICAO Carbon Emissions Calculator, per passenger, Economy Class