GRP pipe liners have been established in the wastewater sector for decades. For a few years now, they have increasingly been introduced into the drinking water sector. Hygienic, sustainable and project-safe—GRP hose liners must meet the highest quality standards for the trenchless rehabilitation of potable water pipes. After all, they ensure the supply of drinking water to many people. For this purpose, drinking water pipes must meet requirements that extend far beyond the gravity sewer sector. They must withstand a nominal pressure of up to 16 bar in the long term and meet high hygienic standards. After an intensive development phase, SAERTEX multiCom® brought the world's first UV-cured GRP pipe liners for trenchless rehabilitation of potable water lines to market maturity with the SAERTEX LINER® H2O and has already presented it at the IFAT in 2016. Fundamental to this were significant adaptations to the existing products and further new developments of the entire liner design, the different test methods and the connection technology.
Names for the inner foil / inner coating of pipe liner
|
|
---|---|
PE/PA inner pipe foil, which is pulled out after installation | Temporary inner foil |
Inner coating, installation and remaining in liner | Semi-permanent inner foil |
Inner coating, integral part | Permanent inner foil |
Fig. 1: Old and new names
Technical and hygienic requirements
In 2008, the SAERTEX multi-COM team began developing the first GRP pipe liners, which had a so-called inner coating with an integrated styrene barrier. Since then, liners with this structure have been successfully used worldwide for trenchless sewer rehabilitation of free-flowing pipes. Inner-coated pipe liners have been on the market for decades in the form of felt liners. With felt liners, however, there is no barrier function.
In contrast, this barrier function is essential for UV-cured GRP pipe liners in order to ensure the
high shelf life of up to six months for the impregnated GRP pipe liners. During this time, the integrated barrier ensures that the styrene remains completely in the resin and does not diffuse through the inner coating. This ensures the subsequent successful curing with UV light. With the launch of this new product, further liner products with different pipe inner films and inner coatings became available. The differences are not only in the presence or absence of a barrier function, but also in the function and durability of the coating in the installed state. Usually, a distinction was made between an inner coating as an "integral component" and an "installation aid remaining in the liner." As these terms were not clearly defined, the working group responsible at the ISO level developed a definition that is clearly defined in the issue of DIN EN ISO 11296-4 from September 2018. In this context, the names temporary, semi-permanent and permanent inner foil were introduced (Fig. 1).
A permanent inner foil is used for potable water lines. This means that the inner film performs a function over the entire technical service life. In contrast to this, the durability of semi-permanent inner films is not required. The development of the permanent interior film with a barrier function was the first major building block for the realization of the potable water liner. Further development steps were necessary until the product was ready for market use, as a potable water pipe places significantly higher demands on rehabilitation products than a free-flowing pipe. On the one hand, these are pressure lines with a nominal pressure of up to 16 bar. Previous liner designs were not suitable for such high pressure, which meant they could not be used to produce PN 16 pipe liners. On the other hand, the selection of raw materials to be used is restricted for hygienic reasons. In order to obtain a German potable water approval, for example, all materials used must be on special positive lists. A special criterion was therefore the choice of a suitable reactive diluent for the resin. Resins with styrene have been successfully used as reactive diluents for GRP pipe liners for rehabilitation in the wastewater sector for decades. Styrene is on the positive list, but due to its low odor threshold, it is not used in the potable water sector.
Development of a GRP pipe liner for potable water pipes
As part of the development phase, SAERTEX multiCom's goal was to adapt all materials to meet the approval requirements for potable water pipes and also to meet the technical and hygienic requirements. In the process, the advantages of the GRP pipe liner at that time were to be retained. These include, for example, factory impregnation, the long storage stability of the liners, and use of installation technologies established in the market.
Further development of the non-crimp glass fabric
In the first step, the strength of the liner design had to be significantly increased against internal pressure. As a subsidiary of the fabric manufacturer SAERTEX®, the application-related further development of technical textiles is a core competence of the entire SAERTEX® Group. With this know-how, the non-crimp glass fabric was further developed to meet the market requirements. The planned strength for practical use was verified using the results of burst pressure tests. A burst pressure test is a failure test that determines the maximum pressure until the pipe liner bursts.
Development of a styrene-free resin system
Together with its resin supplier, the in-house laboratory team also developed a resin system that meets technical and hygienic requirements for potable water pipes. As a reactive solvent, styrene as a monomer was replaced by low-odor acrylates. While there was already a great deal of experience with styrene and its interaction with other liner components, the use of acrylates was still new. The development was not to result in any loss of quality in terms of technical aspects. Therefore, a comprehensive series of tests was conducted in which the effects of the new styrene-free vinyl ester resin (VE resin) with acrylates were thoroughly tested on existing liner components. Over a period of more than six months, the internal laboratory investigated the effects of the styrene-free VE resin on the durability of the inner and outer films. These tests were used to rule out layer separations and embrittlement. In cooperation with an external analytical laboratory, it was also possible to ensure that the barrier function of the inner film also works with acrylates without restrictions. These developments were decisive for obtaining German potable water approval in 2015. In total, SAERTEX-LINER® H2O now has approvals for use in potable water pipes in twelve countries—including China, the USA and Spain.
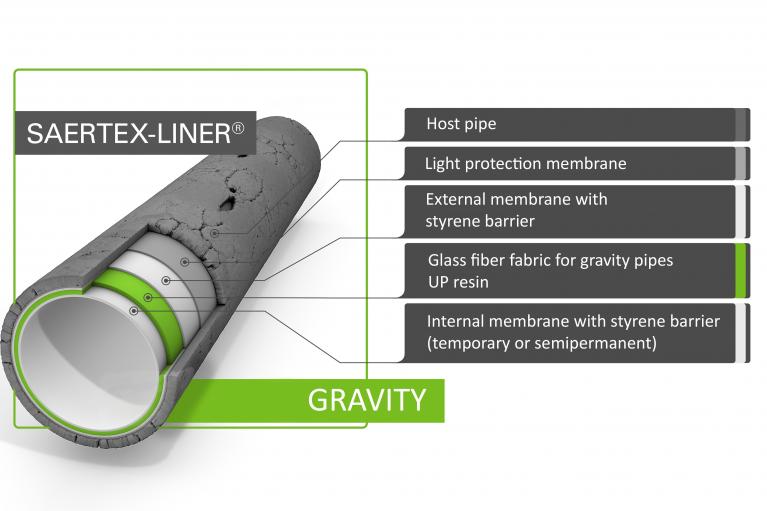
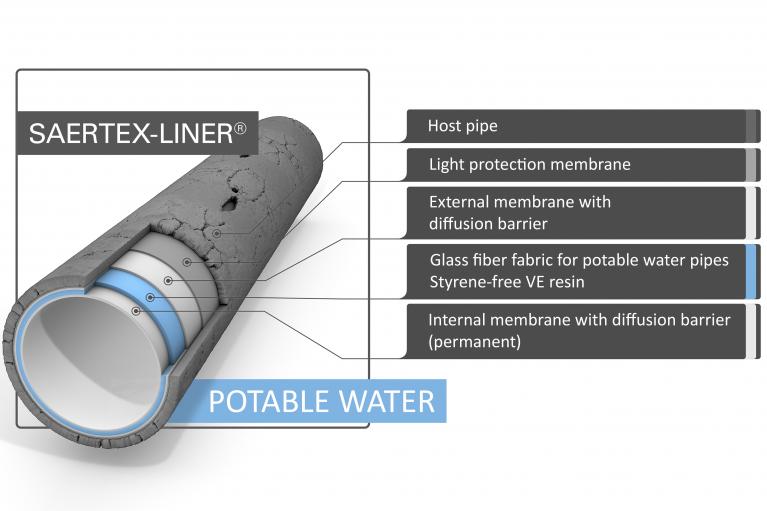
Type tests for potable water liners
The requirements of the network operators were the focus of all development steps from the very beginning. For this reason, the type tests were designed to meet the conditions prevailing in the pipeline networks to be rehabilitated.
These tests allow manufacturers to identify maximum operating pressures per dimension for their liners. Standardized test procedures have already been established for pressure water liners and have been anchored in DIN EN ISO 11297-4 in cooperation with network operators, users, test institutes and manufacturers. These findings are currently being carried over to the potable water sector by the creation of DIN EN ISO 11298-4 for that potable water sector. The time-to-rupture internal pressure tests play a decisive role in this. In this process, test specimens of a hardened pipe liner are subjected to varying internal pressures, and then the process waits until they fail. Failure must occur at different times. For example, at least one test specimen must withstand a certain internal pressure for more than 10,000 hours. This corresponds to a period of 13.8 months. The SAERTEX-LINER H2O met this requirement. In order to create an even larger database, SAERTEX multiCom decided to let a test specimen run for over 47,000 hours (well over five years). Although an internal pressure of 48 bar was permanently applied to the DN 300 liner, no damage to the liner was found after the test was completed.
Ensuring and evaluating the quality of built-in GRP pipe liners
From the very beginning, the safety of the product was the focus, so a market launch was only considered in the case of reproducible quality. In order to ensure this quality on a continuous basis, all information had to be made available to the users, which was also available for all previous products. This includes clear curing parameters for the corresponding combination of pipe liner and curing technology. In order to determine these parameters, test liners are used to check the leak-tightness of the test specimen, the achievement of the required mechanical characteristics, and the residual styrene content.
Since no styrene is used as a reactive diluent for resin systems containing acrylate, an analogous verification method had to be established. Therefore, in cooperation with the resin manufacturer and an analytical laboratory, a test method for the determination of the residual monomer content was developed at the beginning of 2014, which has since been used as standard for years. Using a gas chromatographic test method, a pipe liner sample is tested based on DIN 53394-2. The monomer is extracted for this by shredding the sample and dissolving it with dichloromethane. After the other remaining solids have been filtered out, the analysis is carried out in the gas chromatograph in order to then determine the residual monomer content. The lower the residual monomer content, the further the curing of the resin has progressed. The determination of the residual monomer content thus allows the evaluation of the curing quality. As with the determination of the residual styrene content, the method provides installers and network operators with downstream proof of the hardening level of the pipe liner, if the mechanical tests do not lead to a clear result.
Achieving a high curing quality depends on various factors during installation, such as the pull-through speed and the choice of light source. Using the test method described, it was possible to already determine these factors during the development phase of the styrene-free VE resin with the help of test liners. This has led to the development of an installation procedure that is optimally adapted to the product.
Pressure-tight connection of the pipe liner ends
Since potable water lines are pressure lines, a professional connection technology had to be developed for a pressure-tight transition between the SAERTEX-LINER H2O and the rehabilitated section of pipe. The pressure-tight connection is secured by liner end collars (LEC), which are produced on a project-specific basis. Appropriate preparations must be made in advance of the rehabilitation of a potable water pipe. Only with proper preparation can leak-tightness of the pipe of more than 50 years be achieved. For this purpose, at least 0.7 m long flange adapters designed for the working pressure (or a technically equivalent solution) must be firmly attached to the open ends of the pipe section to be rehabilitated (Fig. 3).
After the successful installation of the pipe liner, the liner ends are then connected. In the first step, a liner cut-back of approximately 10 – 11 cm is made in the pipe for this. (Fig. 4) In a further step, a narrow strip of a specially manufactured sealant is applied along the cut edge for sealing (Fig. 5). The LEC is then installed. The assembly is always carried out with three stainless steel rings (tension band, support band, tension band) (Fig. 6). Maximum operating pressures of 25 bar can be achieved with the built-in sleeves (Fig. 7). In addition, they are suitable for any underpressure and external loads that may occur. Pipe elements (called flange pipes) from different manufacturers can be connected to the connected flange adapters (Fig. 8). After the pipe liner has successfully passed a pressure test, nothing stands in the way of restarting the potable water supply of the pipe section.
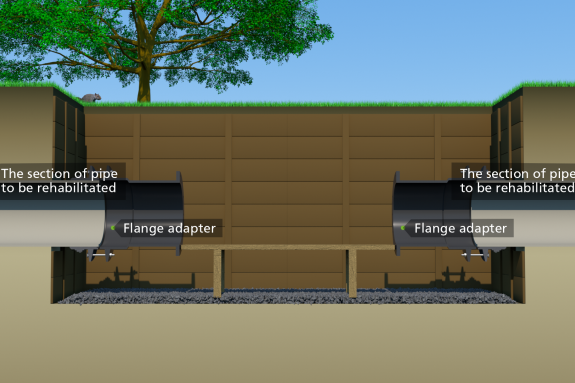
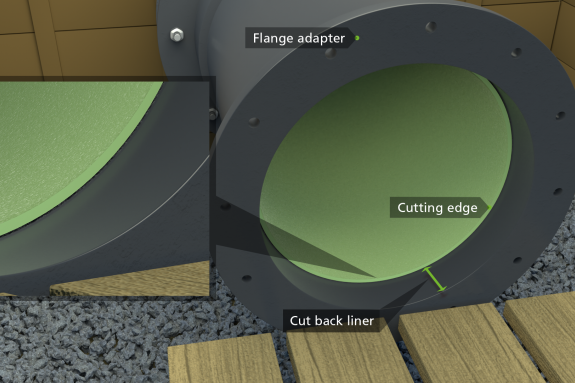
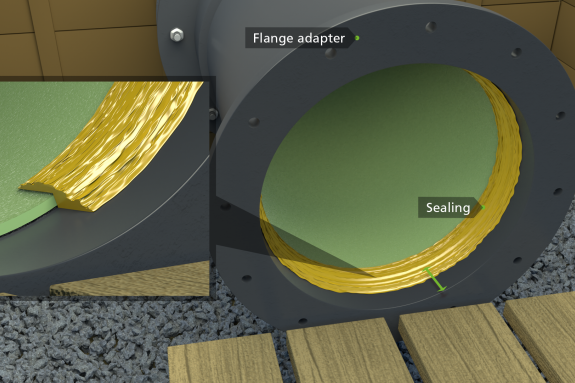
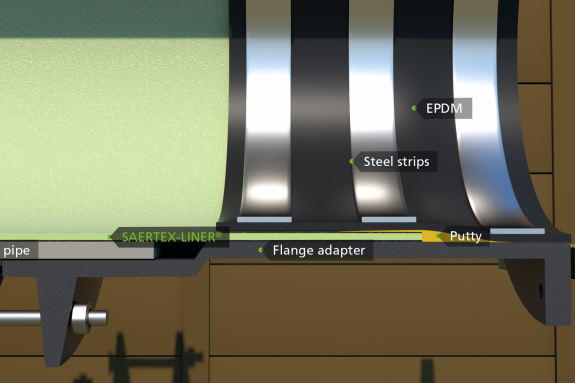
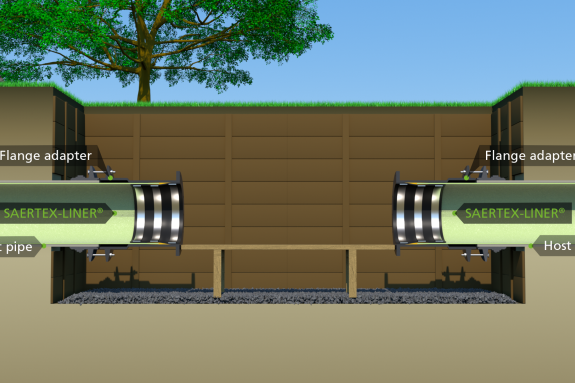
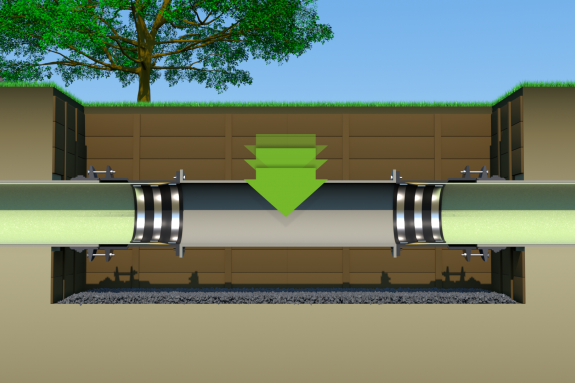
More than 500 m of potable water pipe installed in Valencia
In Dresden, Valencia and Shanghai—with 100 projects and more than 350 installations—network operators worldwide now rely on SAERTEX multiCom products for the rehabilitation of potable water lines.
In Valencia, Spain, for example, the successful installation of SAERTEX LINERs H2O in late summer 2020 ensured the supply of potable water to over 1.6 million people. The trenchless pipe rehabilitation of the 500 m pressure line is thus the largest project of this kind on the Iberian Peninsula to date. The repair was necessary due to the urgently needed rehabilitation of the existing DN 600 cast iron pipe. The network operator EMIMET stated that the main criteria for the upcoming rehabilitation work were: cost-effectiveness, sustainable rehabilitation with a technical service life of 50 years, marginal road and ground work, and maximum project safety. The project was thereupon awarded to GRUPO CANALIS, a Spanish company specializing in trenchless rehabilitation, in combination with the SAERTEX-LINER H2O from SAERTEX multiCom.
Author
Dr. Nils Füchtjohann
Global Director Products